Aerospace cables are specifically designed for aircraft and aeronautical applications. They are characterized by high reliability, great strength and lightness. Aerospace cables are commonly used for signal transmission, data applications and in-flight entertainment. Commonly used data cables in aircraft include fiber optic cables, Ethernet, USB, digital video interfaces and serial SATA data cables. They must meet additional standards and specifications, what makes them different from ordinary cables.
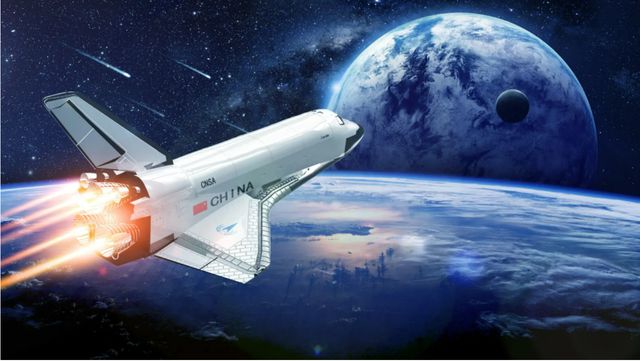
Aerospace cable production process
The aerospace cable manufacturing process involves several key steps to ensure that the cables meet the high reliability and performance requirements of the aerospace sector. Here are some key points of the aerospace cable manufacturing process :
Processing of electrical connectors
All electrical connector housing wires and shield wires are attached together with the wire harness. Attached wire junction points are coated with conformal varnish to improve cable protection.
The blank points of electrical connectors are not tin-plated and are covered with a transparent heat-shrink protective material to prevent oxidation and contamination.
Before welding the golden cups of the electrical connectors, a tinning degold process is carried out to ensure the stability and reliability of the connection. ( Tinning involves covering the ends of copper wires with a thin layer of tin to protect them. )
Cable identification
Cable and electrical connector numbers should be labeled at a distance of 6 has 7 cm from the base of the electrical connector back cap. What's more, full protection with transparent heat shrink materials should be used to protect the cables, thus facilitating their identification and management.
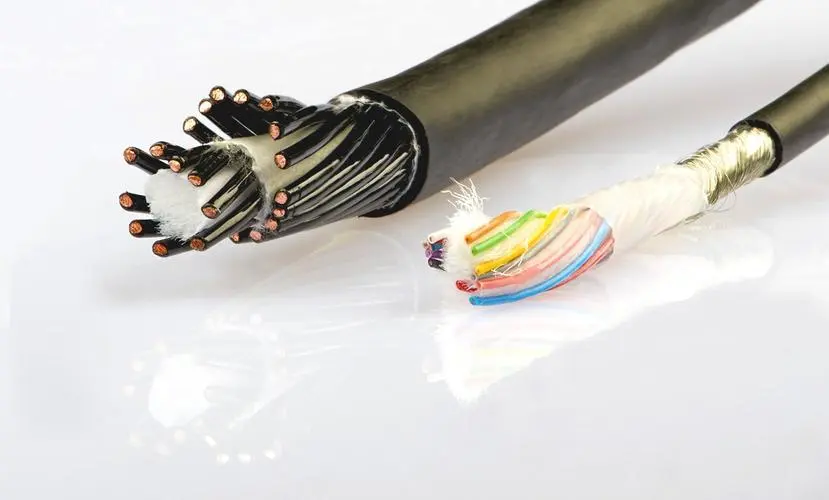
Attaching the beams
To guarantee compliance with production deadlines, bundles can be tied with ropes or transparent heat shrink materials in segments. The spacing between the fasteners must be 150 has 200 mm to keep the beams tidy and secure.
Armor treatment
Two protection methods are used : the use of shield shells and the connection of shield wires to the shells. This improves the effect of electromagnetic cable shielding and reduces electromagnetic interference.
Manufacturing process
Although the manufacturing process may vary depending on the cable type and specifications, it generally includes the following steps : treatment of drivers, injection of insulation, pressure resistance test, forming cables or adding steel armor, and injection of the sheath. For special cables, special techniques such as high temperature F46 injection or silicone rubber insulation may be required to meet specific aerospace performance requirements.
Aerospace cable manufacturing process emphasizes details and special requirements to ensure cable reliability and safety in extreme environments.
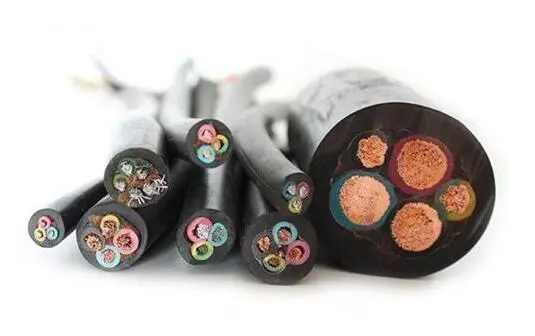
Aerospace cable characteristics
Aerospace cables are special cables mainly used in harsh environments such as aerospace, military and marine equipment for connecting electrical equipment, instruments and transmission of high frequency signals. They use fluoropolymer insulation (series AF-250, FF46-2, SFF, etc.). These cables have excellent electrical and mechanical performances. Here are some of their main features :
Resistance to extreme temperatures : Aerospace cables must operate in extreme temperature conditions. They therefore offer excellent resistance to high and low temperatures. Their operating temperature range extends from -65°C to 250°C.
Corrosion and vibration resistance : The aviation environment contains various corrosive substances and strong vibrations. Aerospace cables must therefore be resistant to corrosion and vibrations. They must also be resistant to wear, aging and radiation.
Lightness : Aircraft have strict weight restrictions. Aerospace cables typically use lightweight materials to reduce the overall weight of the aircraft. Therefore, these cables are characterized by reduced volume and light weight. To facilitate their use, they are also designed to be easy to install.
High reliability : Aerospace cables must be extremely reliable and have a long lifespan to ensure flight safety.
These features make aerospace cables an essential choice for critical applications in demanding environments.
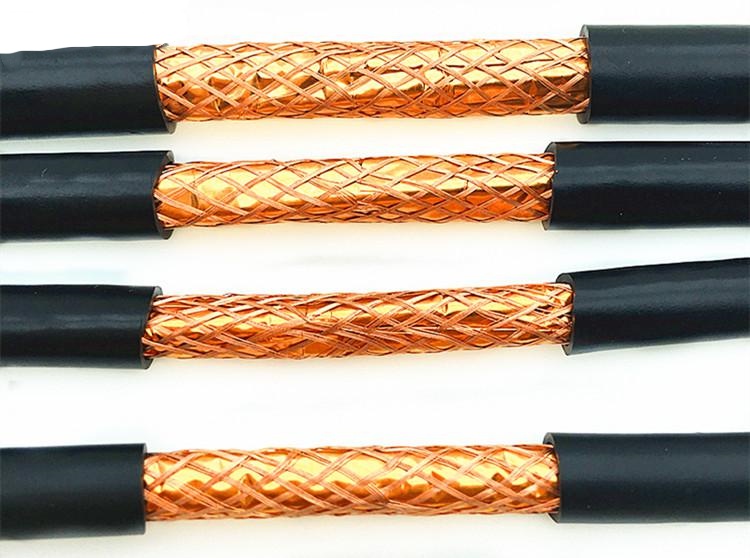
Types of Aerospace Cables
Aeronautical installation cables are used in aircraft, helicopters, spacecraft and other aeronautical equipment. They include flame retardant cables, shielded cables, radiation resistant cables, etc.
Shielded cables
Shielded cables are cables whose conductors are completely isolated from the outside world. They reduce electromagnetic interference that can affect cables. This guarantees the stability of the cables. In aeronautical equipment, shielded cables are generally used for transmitting signals and connecting computer networks.
Flame retardant cables
Flame-retardant cables are cables capable of extinguishing themselves in the event of a fire. They allow aeronautical equipment to extinguish quickly in the event of a fire, thereby reducing fire hazards. Fireproof cables are typically used for power and signal transmission in aircraft.
Radiation resistant cables
Radiation-resistant cables can reduce the impact of high-energy radiation on cables, thus ensuring their stability. In aeronautical equipment, These cables are commonly used for satellite communications and navigation systems.
Selection of aviation cables
The safety and stability of spacecraft and other aeronautical equipment are inseparable from the support of aeronautical cables. For the selection and installation of aeronautical cables, it is necessary to take into account the particular characteristics of the environment in which they are located, as well as cable stability and interference suppression requirements. Different types of aeronautical cables have different application scenarios in aircraft and should be selected according to specific needs.
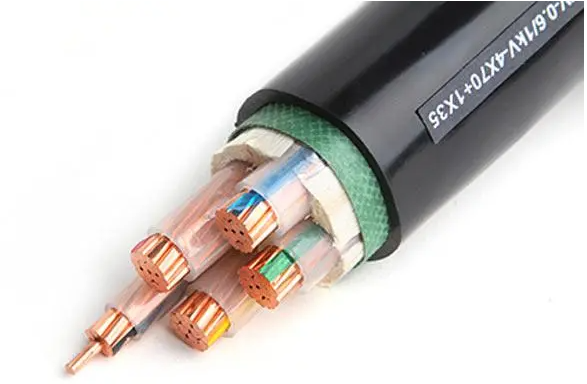
So what are the main elements to take into account when choosing aeronautical cables? ?
First of all, the main function of the cable must be taken into account, of its environment and the challenges it may face (For example, the temperature, exposure to liquids, the movements required). This aspect is particularly important for aeronautical cables. Indeed, they may need to operate in a wide range of temperatures and atmospheric pressures, and will be exposed to numerous movements and vibrations during takeoff and landing.
Secondly, you must consider all required industrial specifications. You should ensure that the cables you choose meet these guidelines. Quality, the safety and performance of the different materials used in the cable are particularly important.
Thirdly, you may need to take extra precautions if the plane is carrying passengers. Low smoke cables and halogen-free (LSZH) are part of the standard equipment of any manned aircraft. In case of fire, These cables produce little or no smoke and no dangerous gases from halogens. As most planes are enclosed and have limited ventilation, LSZH cables make evacuation easier and safer.
Taking these standards and requirements into account will help select the most appropriate cables and reduce possible replacement and repair costs..
ZMS Cables is committed to producing high quality cables. With more than 30 years of experience in the cable industry, ZMS is dedicated to manufacturing high-end cables by strictly controlling their quality. ZMS Cable has its own cable factory and offers customization services, able to produce any cable that meets your requirements. For more information, you can visit our official website or send an email to info@zmscable.fr.