Insulation materials are used as the insulating layer of the cable to insulate the stranded conductors and the interactions between the conductors and the sheath. They also provide a certain resistance to tension, a certain resistance to heat and a stable insulation quality.
The thickness of the insulation layer is related to the operating voltage. Generally speaking, the higher the voltage level, the thicker the insulation layer, but it is not proportional.
Due to the intensity of the electric field, the thickness of the insulation layer can be lower for cables of the same voltage level when the cross-sectional area of the conductor is larger.
For low voltage cables, especially paper-insulated cables, to ensure cable bending, the paper layer has a certain mechanical resistance, the thickness of the insulation layer should be increased with the increase in the cross section of the conductor.
The materials of the insulation layer are mainly oil-impregnated paper, plastic and rubber.
Depending on the conductor insulation layer used in the different materials, insulated cable is mainly divided into plastic insulated cable, rubber insulated cable and oil impregnated paper insulated cable.
The structure and characteristics of the three types of cable insulation are as follows.
Plastic Insulation
Plastic insulation is an important insulation material, which mainly includes l’isolation PVC et l’isolation XLPE.
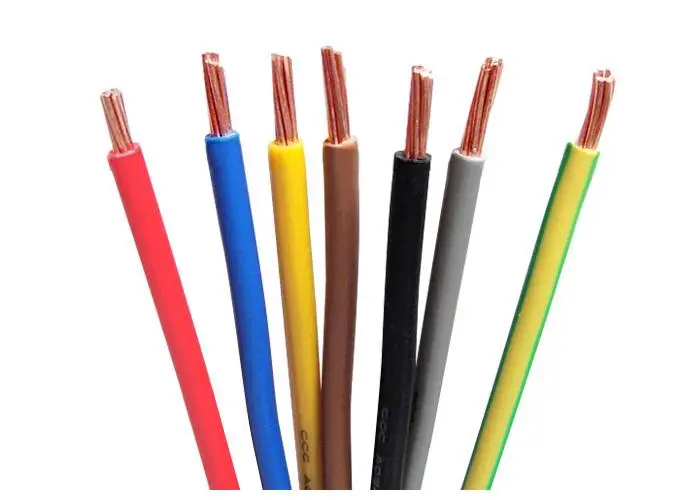
The cable insulation layer is made of extruded thermoplastic plastic, which is cross-linked by adding a cross-linking agent after extruding the thermoplastic PVC plastic.
This type of insulation has good electrical properties and good water resistance., can resist acids and alkalis, prevents corrosion, but also has the advantages of high operating temperature, good mechanical properties and can be used for the manufacture of high voltage cables.
Insulation a Caoutchouc
THE rubber insulated electrical cables are insulated with styrene-butadiene rubber or synthetic rubber.
The main advantages of these cables are their flexibility and good weldability, which makes them particularly suitable for mobile energy and electricity supply installations.
However, rubber insulation is quickly damaged when it comes into contact with oil.
This is due to the effect of high voltage, which cracks due to the sensitivity of the material to the corona effect.
Therefore, These cables are generally used for medium voltage insulated cables up to 10 kV and less, while cables insulated with ethylene-propylene synthetic rubber are used for voltages up to 35 kV.
Insulation a Papier Iimpregnated with’Hall
Oil-impregnated paper insulation consists of a combination of cable paper and impregnating agent.
The thickness of normal cable paper insulated with oil impregnated paper is 0,08, 0,12 et 0,17 mm.
The impregnating agent is mixed with low voltage cable oil and rosin and is called viscous impregnated cable oil.
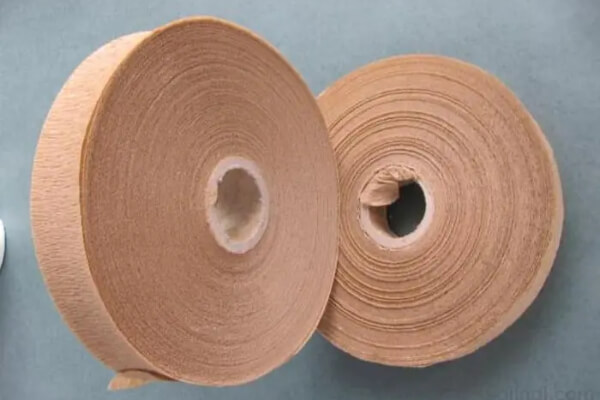
Construction de l’isolation
Single-core cables and lead-sheathed cables (aluminium) separated phases have a circular conductor and the insulation consists of a strip of paper wound in concentric layers in the shape of a circle.
THE 10kV multi-conductor cables and less, the conductor is semi-circular, oval or fan-shaped, the structure of the insulation layer is ribbon-bundle type.
This structure is as follows : each conductor is wrapped around part of the insulating paper, several conductors are wound together, then wrapped around some thickness of cable paper, known as total package insulation or tape insulation.
In this way, the thickness of the insulation between the conductor and the conductor is twice that of the conductor.
Between conductor and conductor sheath, the thickness of the conductor insulation is added to the thickness of the total packaging insulation.
Oil-impregnated paper insulation of oil-filled cables requires high electrical performance, a paper thickness of 0,045, 0,075, 0,125, 0,175 mm and so on, the value of the tangent of the dielectric loss angle must be greater than 0,0026.
Low viscosity oil impregnation, the breaking strength of the oil frequency should not be less than 60 kV/2,5 mm.
This significantly improves the electrical resistance of the cable insulation under a certain oil pressure.
Factors Aaffecting the Thickness of the’Isolation
The thickness of the cable insulation material is determined by the operating voltage of the cable and the nominal cross section of the conductor, both to ensure that frequency voltage and shock voltage are not broken, but also to ensure that the insulation is not mechanically damaged in normal construction.
Oil-impregnated paper insulation is more heat resistant than rubber insulation and polyethylene insulation ; the working temperature can generally reach 80°C and the electrical resistance is high.
Voltage levels less than or equal to 35 kV are insulated with adhesive oil-impregnated paper insulation, while voltage levels greater than or equal to 60 kV are insulated with oil-impregnated paper insulation.
Paper insulation easily absorbs moisture, which significantly reduces the resistance of the insulation. This is why, in addition to dehumidification and impregnation, a metal sheath is used to prevent moisture penetration.
Furthermore, paper insulation being relatively inflexible, the minimum permitted bending radius and the minimum cable laying temperature are specified.
For these reasons, special precautions should be taken during construction to ensure good insulation properties.
PVC insulation
PVC insulation has many advantages over oil-impregnated paper insulation, but its dielectric loss is significant, environ 10 has 20 times that of oil-impregnated paper insulation.
Furthermore, its conductivity increases sharply with the intensity of the electric field, which limits its use to higher voltages.
Under the same conditions, the alternating current breaking strength of PE is approximately 60 % higher than that of PVC, and the dielectric loss only represents 0,5 % from that of PVC.
PE insulated cables are characterized by high insulating properties, low density, good resistance to water and chemical corrosion, but their melting point is so low that they crack easily under mechanical stress.
In order to utilize the good insulating properties of polyethylene and overcome the disadvantage of its low melting point, polyethylene can be cross-linked.
Polyethylene can be crosslinked by high energy irradiation or chemical methods, so that its molecules change from the original linear structure to a reticular structure, i.e. from thermoplastic to thermosetting, thereby improving the heat resistance and thermal stability of polyethylene, who is XLPE.
The main characteristics of XLPE insulation material are high softening point, low thermal deformation, high mechanical resistance at high temperatures, good resistance to thermal aging, etc. The maximum operating temperature of cross-linked polyethylene cables can reach 90°C, and the admissible short-circuit temperature 250°C.
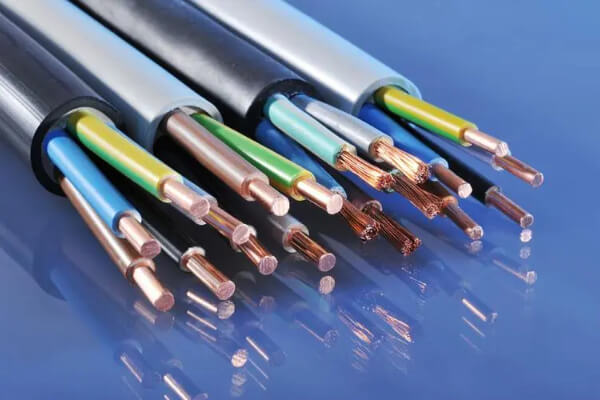
Although the cable has very superior electrical properties, there are inevitably micropores, impurities and other defects inside the insulating layer.
Especially, the presence of micropores promotes water absorption, which triggers the phenomenon of “water dendrite” along the direction of the electric field under the action of a high electric field and damages the insulation.
Actually, selection of insulation material and control of micropores and impurities during the manufacturing process are the main ways to reduce the water dendrite phenomenon, but unreasonable construction methods during installation can also lead to the formation of new micropores.
ZMS offers insulated cables with excellent insulation properties. The selection of insulation materials is based on what is best to obtain the best insulation properties.