Copper cables play a vital role in the transmission and distribution of electricity. Understanding the current carrying capacity of copper cables is crucial for electrical engineers and everyday users. It's not just about cable performance and lifespan, but also has a direct impact on safety during their use. This article explores in detail the current carrying capacity of copper cables and the factors that influence it, to guide you in the choice and use of these cables.
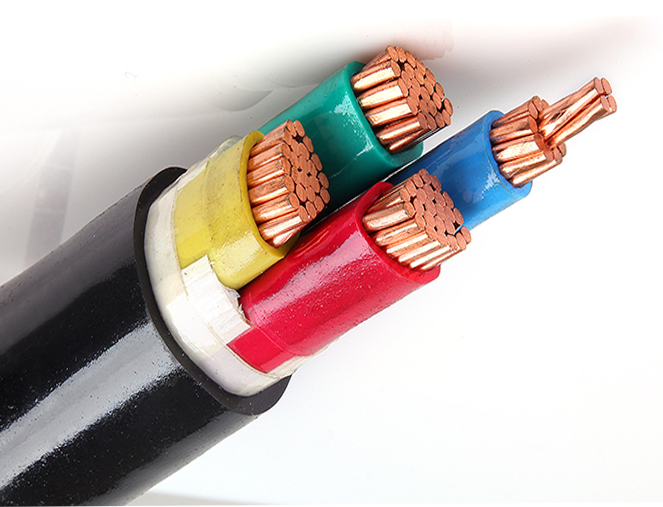
Introduction
Copper cables are widely used in various electrical and engineering works due to their excellent conductivity and mechanical strength. Whether for domestic wiring, industrial equipment or large-scale electrical infrastructure, copper cables are essential. Choosing the right specifications and type of cable not only optimizes the performance of the electrical system, but also to effectively prevent the risks of overloading and overheating. To ensure the safety and reliability of cables in different applications, it is essential to understand their current carrying capacity.
Current carrying capacity of copper cables
The current carrying capacity of a cable is defined as the maximum current that the cable can withstand under safe operating conditions. This criterion depends on many factors, in particular the cross section of the cable, the type of material, the insulation material, ambient temperature and installation method. Properly choosing and using copper cables can effectively reduce system losses, improve operational efficiency and avoid overheating and cable damage issues.
Main factors influencing the current carrying capacity of copper cables
Cable cross section
The cross section of a cable is one of the key factors that determine its current carrying capacity. In general, the larger the cross section of the cable, the more current it can handle. This is explained by the fact that a larger section reduces the resistance to the flow of current, thus reducing energy losses. For example, a copper cable with a section of 2,5 mm² can support approximately 21 A, while a cable of 10 mm² can transport up to 57 A.
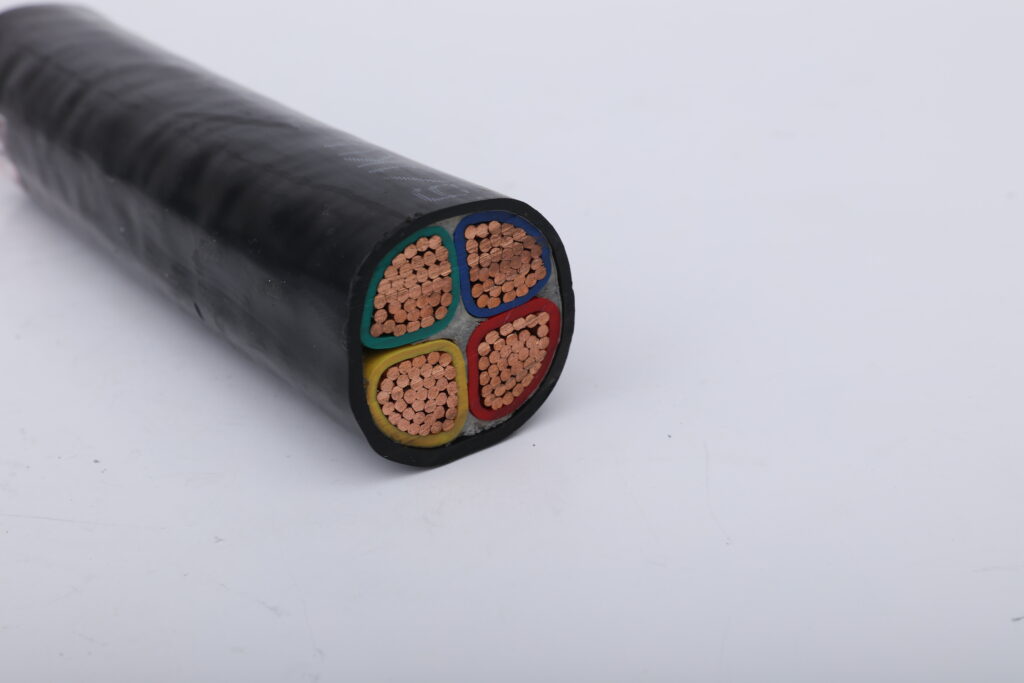
Temperature conditions
The ambient temperature and temperature rise of the cable also have a significant impact on its current carrying capacity. Generally, the higher the temperature, the more the current carrying capacity of the cable decreases. This is because high temperature increases the resistance of the cable material, thereby reducing the amount of current it can safely carry. Therefore, in high temperature environments, it is often necessary to use cables with a larger cross-section or with special insulation materials to meet current requirements.
Cable installation method
The cable installation method (For example, buried directly, suspended in the air or placed in a conduit) also influences its heat dissipation capacity and, therefore, its current carrying capacity. Directly buried cables generally have a lower current carrying capacity than suspended cables due to less favorable heat dissipation conditions. It is therefore essential to choose the appropriate installation method for each type of cable.. Ensuring good heat dissipation is crucial to optimize current carrying capacity.
Insulation and sheath materials
Insulation and sheath materials have different thermal stability and heat resistance properties, which may affect the current carrying capacity of the cable. High-quality insulation materials can improve the thermal resistance of the cable, allowing it to remain stable even under high currents. On the other hand, Less heat-resistant materials may limit the current-carrying capacity of the cable.
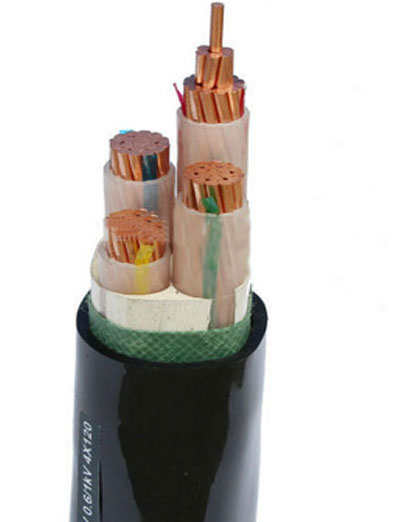
Cable standards and regulations
The current carrying capacity of copper cables is clearly defined in different electrical standards and regulations, such as those of the International Electrotechnical Commission (the), d’Underwriters Laboratories (UL) and the National Electricity Code (NEC). These standards and regulations provide detailed guidelines for cable selection, helping users select the appropriate cable section and type based on their specific needs and application conditions.
Method for Calculating the Current Carrying Capacity of Copper Cables
Calculating the current carrying capacity of copper cables is usually based on basic electrical principles such as Ohm's Law and Joule's Law. Here is the formula :
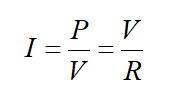
where I is the current, P is the power, V is voltage and R is resistance.
Let's take an example. Let's assume a copper cable with a section of 4 mm², at an ambient temperature of 20°C, and a resistivity of 0,0178 Ω·mm²/m. If the cable length is 100 meters, then the resistance R is calculated as follows :

According to the formula, the current I is then :
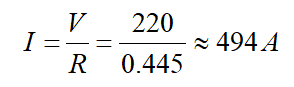
However, this is a theoretical calculation. In practice, Various correction factors must be taken into account to obtain more accurate results.
Table of current carrying capacity of common copper cables
Section transversale (mm²) | PVC insulated cable (A) | XLPE insulated cable (A) |
1.5 | 15 | 18 |
2.5 | 21 | 24 |
4 | 28 | 32 |
6 | 36 | 40 |
10 | 50 | 55 |
Application examples of current capacity of copper cables
In household wiring, to ensure the safety and stability of the power supply, we generally choose copper cables of 2,5 mm² ou 4 mm². On the other hand, in industrial equipment and electrical installations where current requirements are higher, copper cables 10 mm² or larger cross section are commonly used. A bad choice, such as insufficient cable section for high current, can cause overheating, damage to insulation, or even cause a fire.
Safety and maintenance tips
When choosing and installing copper cables, It is essential to strictly follow electrical norms and safety standards to ensure that the current carrying capacity of cables meets actual needs. Furthermore, regularly inspect the condition of the cables, especially insulation and connections, can effectively prevent aging and damage, thus ensuring safe and reliable long-term operation.
Advantages of copper cables produced by ZMS
ZMS copper cables are recognized for their exceptional performance and reliability, making it the preferred choice for many electrical systems and electrical engineering projects. Here are some main advantages of copper cables: ZMS Cable:
Excellent conductivity
ZMS copper cables are made from high quality copper, with very low electrical resistance, ensuring efficient and stable power transmission. This exceptional conductivity reduces energy loss and improves overall system efficiency.
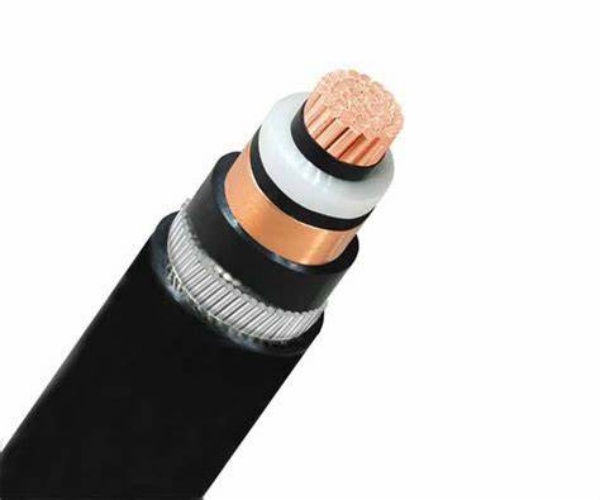
Excellent mechanical resistance
Our copper cables are robust and can withstand significant tensile and bending loads. Whether in harsh environmental conditions or under high loads, ZMS copper cables show remarkable performance, ensuring long-term reliability.
Excellent corrosion resistance
ZMS copper cables have excellent corrosion resistance. They are suitable for humid and corrosive environments. This corrosion resistance allows cables to maintain stable performance in extreme conditions, thus extending their lifespan.
Ease of installation and maintenance
Thanks to their great flexibility and extensibility, ZMS copper cables are easy to install and can adapt to various configurations. What's more, they have a long lifespan, which reduces long-term operating costs.
High security
ZMS copper cables are stable in case of overload and short circuit, reducing the risk of overheating. We also conduct rigorous safety testing to ensure safety and reliability under various working conditions.
Customization options
ZMS offers custom copper cables, designed according to specific customer needs, in particular the section, the insulation material and the type of sheath. This customization option ensures that each project gets the most suitable cable, meeting specific technical requirements and application environments.
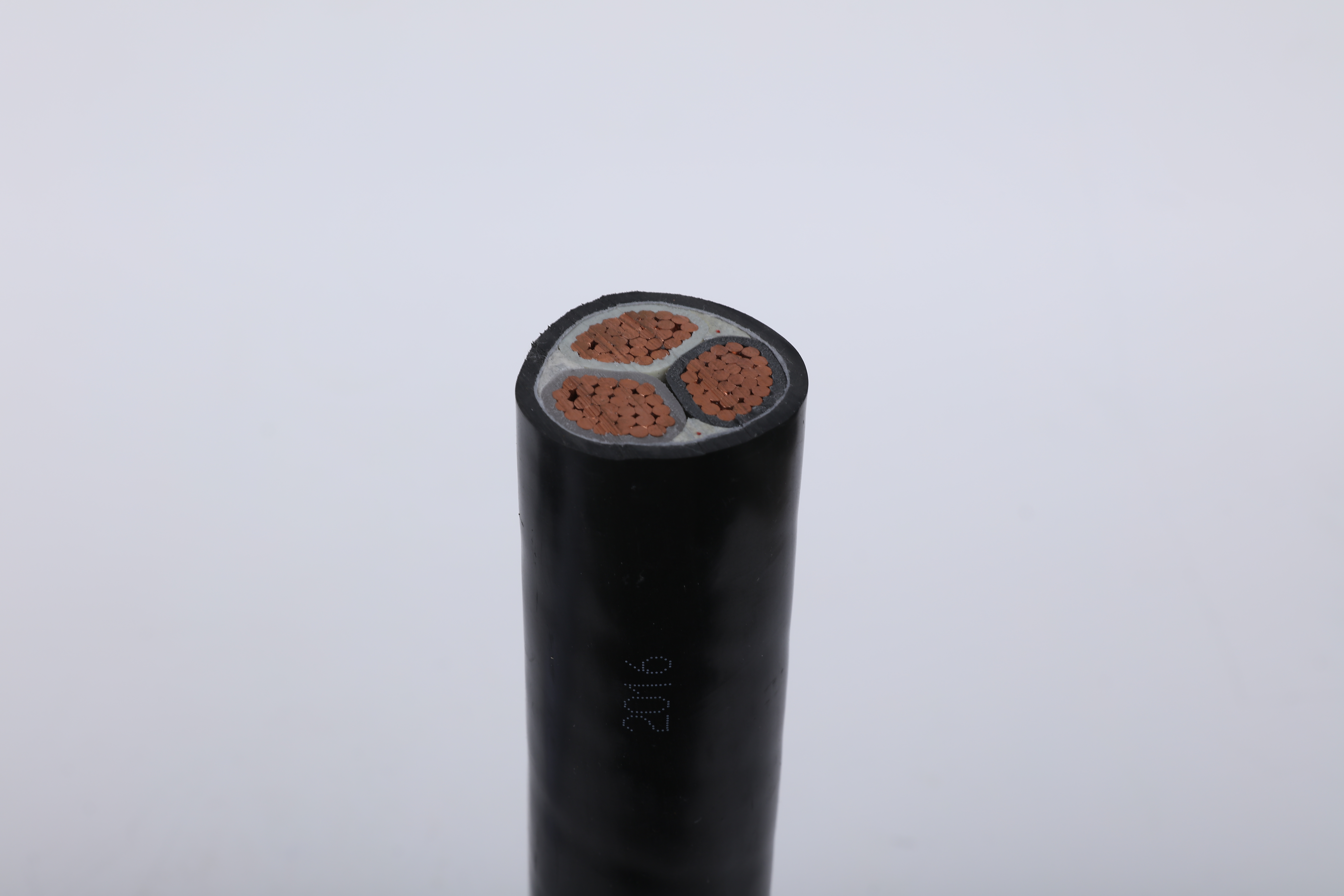
Compliance with international standards
ZMS copper cables meet various international electrical standards (like IEC, UL), ensuring consistent product quality and performance. This allows our cables to be widely used around the world, meeting the needs of different markets and customers.
Thanks to these advantages, ZMS copper cables provide reliable power transmission solutions in various application contexts, ensuring efficient and secure operation of the system. Whether for a domestic electrical installation or a complex industrial project, copper cables produced by ZMS are a trusted choice.
Conclusion
The current carrying capacity of copper cables depends on several factors, in particular the section of the cable, temperature conditions, the method of installation and insulation materials. When choosing and using copper cables, it is important to take all these factors into account, rigorously calculate and select in accordance with standards to ensure cable safety and reliability.